Robot-Ready Floors: The New Standard for Industrial Concrete
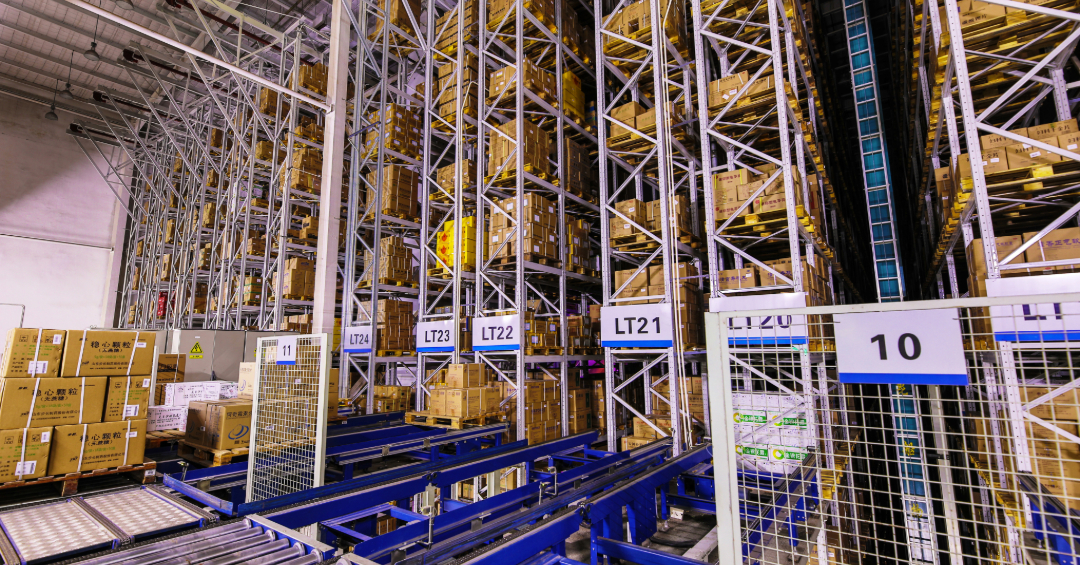
Ever poured a floor that hits every spec, only to realize it’s not enough for robots?
Here’s the deal: warehouse automation is here, and it’s seriously changing the game for concrete specs. Recently, I had a lunch with a friend, and we were talking about Walmart's push to overhaul their distribution centers with automated rack systems. What caught my attention was the scale of it all – 42 of Walmart’s distribution centers are being renovated to accommodate robotics and automated storage systems. And this is happening at an industry-wide scale. In fact, over 50% of U.S. companies are already implementing or planning to implement some form of warehouse automation in the next 5 years. So, what does this mean for concrete?
You guessed it – robot-ready floors are now a must.
In Episode #121 of the Concrete Logic Podcast, I talked with Derek Cressman, President of Durable Surfaces, about how FF/FL ratings (the old standard for floor flatness and levelness) just don’t cut it when you’re dealing with robots. It turns out the precision needed for automation goes way beyond what standard concrete specs offer.
When FF/FL Just Isn’t Enough for Robots
For years, we’ve relied on FF (flatness) and FL (levelness) numbers to measure a floor’s quality. Contractors hit these numbers, and everything seems fine, right? Well, not quite. In the world of warehouse robotics, those numbers are just the starting point. Here’s the kicker: FF/FL measures are a statistical sample of the floor, not the entire slab. This means there could be tiny, localized bumps or dips that pass under the radar but will throw off automated systems that need near-perfect precision. Derek shared that robot manufacturers often have much tighter tolerances than we do here in the U.S., and owners typically don’t realize this until it’s too late.
I’ve heard stories from project teams where the FF/FL spec was met, but the robots still couldn’t function properly. The floor just wasn’t ready for automation. Imagine this: you pour a slab that meets spec, and then the robots break down left and right. It’s a headache that could have been avoided if the floor was prepared for the real demands of robotics.
The Bigger Picture: How Automation is Shaping Concrete Specs
The automation push is massive, and it’s happening at an accelerating pace. More than half of U.S. companies are investing in warehouse automation. As companies shift toward automation, the quality of their concrete floors has become a critical piece of the puzzle. The precision needed for things like robotic forklifts, automated palletizers, and pick-and-place systems is raising the bar on floor expectations.
This is where the traditional FF/FL measurements start to fall short. Robot-ready floors need a more holistic approach to flatness. Derek mentioned that new specifications like F-min floors (often used in highly automated spaces) offer a much higher level of precision. These are “defined-traffic” floors where robots move along specific paths, and the floor needs to meet extremely high tolerances. Without this level of precision, automation can fail—resulting in costly repairs, downtime, and frustrated facility owners.
But it’s not just the big players like Walmart who are leading the charge. Small and medium-sized businesses are getting in on the act too. Automated AGVs (automated guided vehicles) and ASRS (automated storage and retrieval systems) are becoming more common in facilities across the country. And to keep up with the demand, more concrete contractors are learning that simply meeting FF/FL specs isn’t enough. The floors have to be ground and treated to meet the specific needs of robotic systems.
Why It’s Crucial to Get the Floor Right
If you’re involved in a project with automation – whether it’s a new build or a retrofit – you need to start thinking about the floor earlier than ever. The old rule of just hitting FF/FL numbers doesn’t cover the full picture. In fact, 40% of automation failures happen because of floor problems. Think about that – almost half of the time, the floor is the reason robots aren’t functioning as expected.
A prime example that Derek shared with me: a 800,000+ sq. ft. robotics system was only achieving 30% of its intended productivity because of poor floor conditions. After some targeted grinding and repairs, the system’s utilization jumped to 99%. All that productivity was locked up in the floor. Getting it right makes all the difference.
And while it’s easy to think “we can just fix the floor after the fact,” it’s not always that simple. As Derek pointed out, it’s tough to grind a floor that hasn’t cured properly, and timing is everything. You can’t wait until the robots are on-site to start fixing things. If you’re investing in automation, get ahead of the curve. Start working with experts who understand the robotics specs and can deliver a truly robot-ready floor.
Don’t Get Left Behind – Learn More and Prepare
The trend is clear: automation is the future of logistics and warehousing, and it’s reshaping concrete specifications. As we’ve seen with Walmart and other industry leaders, floor precision is now a non-negotiable for high-functioning automated systems.
That’s why the Concrete Logic Podcast and Concrete Logic Academy exist – to keep you ahead of the curve. In Episode #121, Derek and I dug deep into the challenges of creating floors that can accommodate the high demands of robotics. Want to avoid the costly mistakes others have made? Check out the podcast, get the full scoop, and explore the courses at Concrete Logic Academy to make sure your next project is fully prepared for automation.
In this industry, knowledge is power. Make sure your floors are built for the future – not just today.
Listen to Episode #121 of the Concrete Logic Podcast and discover how to ensure your concrete floors are ready for the robots. Then, head over to the Concrete Logic Academy to dive deeper and earn professional development hours while you learn.