EP #121: Robotics’ Impact on Concrete Floors: Are Your Specs Ready?
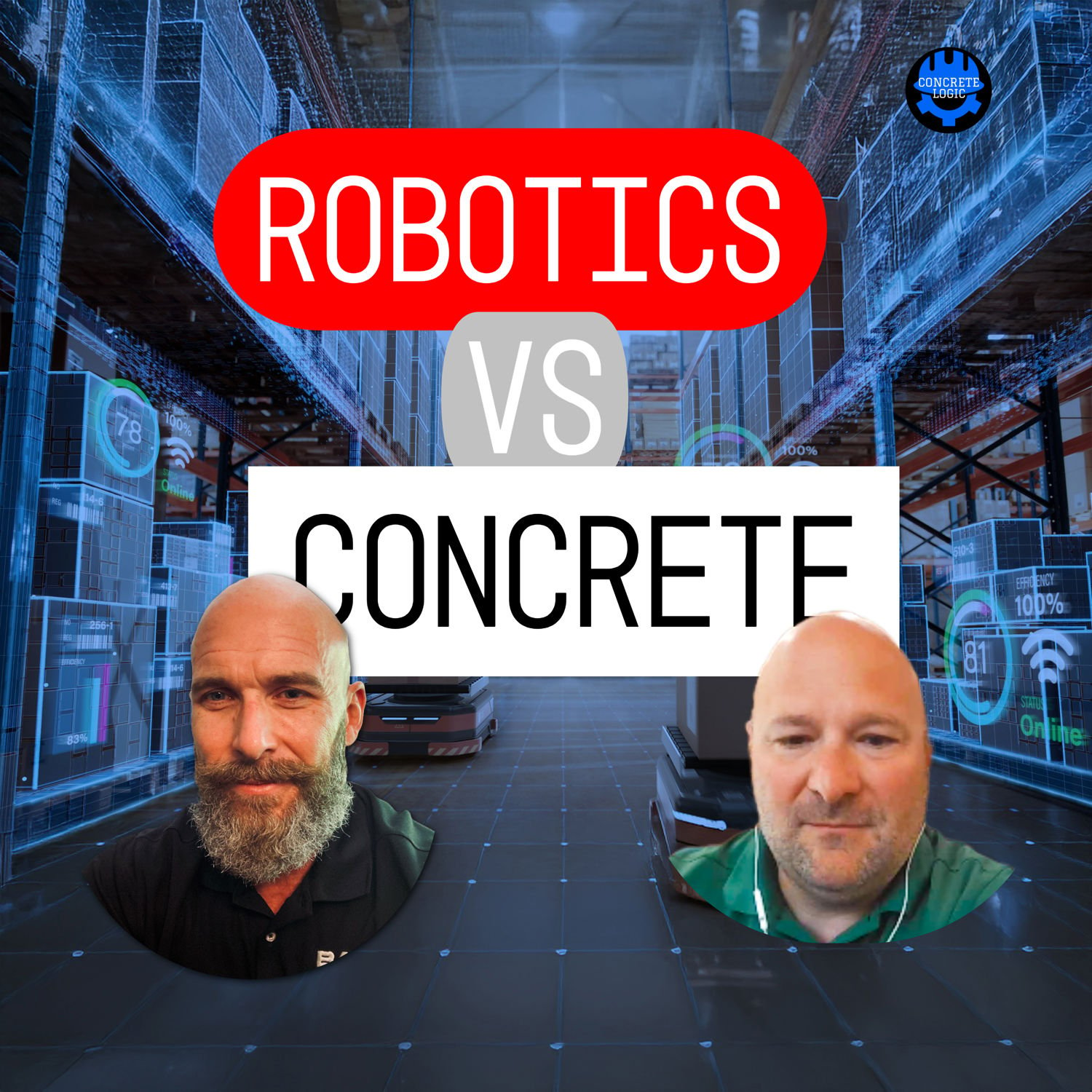
Could your concrete floors be sabotaging your automation systems?
In this episode of the Concrete Logic Podcast, Seth Tandett sits down with Derek Cressman, President of Durable Surfaces, to explore how the rise of automation and robotics is reshaping the way we design concrete floors. They break down the limitations of current FF and FL ratings, why these specs may no longer cut it in industrial settings, and the crucial role floor conditions play in automation success.
Derek stresses the importance of setting clear expectations and maintaining communication between project teams to prevent costly mistakes due to poor floor specifications. If you're in construction or planning for automated systems, this episode is a must-listen.
What You'll Learn in this episode:
- Why are FF and FL ratings no longer enough for modern robotics?
- What exactly are "free movement" floors, and how do they benefit robotics?
- How do "defined traffic" floors impact robotic movement in industrial settings?
- Why is measuring floor flatness more complex than just using a dipstick?
- What specific environmental specs do robotics manufacturers require for floors?
- How can poor floor conditions lead to costly automation failures?
- Why is setting clear expectations in concrete contracts critical for automation success?
- How can better communication between project teams prevent automation issues?
- What can we learn from European practices that might improve our floor specifications?
- Can repairing floors actually boost the efficiency of automated systems?
CHAPTERS:
00:00 Introduction to Concrete Floor Specifications
03:07 Understanding FF and FL Ratings
05:59 Free Movement vs. Defined Traffic Floors
09:04 Measuring Floor Flatness and Levelness
12:03 The Role of Robotics in Floor Specifications
14:57 Challenges with Current Specifications
18:02 Setting Expectations in Concrete Contracts
21:03 The Importance of Communication
23:53 Learning from European Practices
26:55 Automation Failures and Floor Conditions
29:58 Conclusion and Contact Information
LISTEN NOW – Every concrete contractor, architect, engineer and spec writer needs to hear this one!
Guest: Derek Cressman
Company: Durable Surfaces
Website: durablesurfaces.com
Email: derek@durablesurfaces.com
=============================
Take Your Knowledge Further – Join Concrete Logic Academy!
Gain exclusive access to expert video courses, live Q&A, and cutting-edge industry insights. Earn Professional Development Hours (PDHs) and elevate your expertise!
Learn More: https://www.concretelogicacademy.com
Support the Podcast – Be Part of the Concrete Revolution!
Donate: https://www.concretelogicpodcast.com
Become a producer & get recognized on our next episode!
=============================
Producer: Jodi Tandett
Music by: Mike Dunton
Instagram: @Mike_Dunton
Stay Connected & Watch More!
Host: Seth Tandett
Email: seth@concretelogicpodcast.com
LinkedIn: https://www.linkedin.com/in/seth-tandett/
YouTube Channel: https://www.youtube.com/@concretelogicpodcast
Podcast Website: https://www.concretelogicpodcast.com
LIKE, SUBSCRIBE, COMMENT & SHARE for more expert concrete insights!
Seth Tandett (00:00)
And welcome to another episode of the Concrete Logic Podcast. And today I have Derek Cressman, President of Durable Surfaces. And they are a polishing and a dry finishing contractor. Is that correct, Derek?
Derek Cressman (00:14)
Yeah, we kind of sum up the services as repairs and technical grinding.
Seth Tandett (00:19)
Yeah. There you go. Yeah. So today what we're going to talk about, we're going to talk about how do FF and FL numbers shape the concrete floors we rely on today and what they are missing for the future. As logistics and robotics continue to grow, how will the needs for floor specifications evolve beyond FF and FL ratings?
Derek Cressman (00:19)
concrete after it gets hard.
Seth Tandett (00:41)
What's the difference between how the US industry measures floor flatness and levelness versus what robotics and logistics demand for optimal performance? And lastly, how can we ensure our floors are ready for the robots of tomorrow and what new specifications should we be looking at? So Derek, we were discussing before we hit record today,
with the demands of robotics, there's a gap as far as what our specifications are trying to deliver. Because as a concrete guy, you said you're the contractor that works with concrete after it gets hard. I work for a contractor. We work it when it's wet.
Our standard is an FFFL number, but why you're joining us today is as you're saying, for new facilities that have robotics, there's a gap there that we need to fill, and that's where your company comes in. So can you introduce us to that, and we'll get started?
Derek Cressman (01:47)
That's right, Seth. Thanks for having me. Appreciate the time and appreciate the willingness to discuss this topic. So again, my name is Derek Cressman. I'm the president over at Durable Surfaces and one of the partners. And we specialize in the technical grinding and the repair of concrete in industrial facilities.
be it for a regular forklift situation or one of these more advanced robotics programs. What I was talking to Seth about before we started here today was just how much the world is changing in the world of industrial logistics and the types of machinery that they're putting in. And what we're finding really is that FFFL is beginning to...
create a bit of a confusion in the industrial market. The reason being is we have a tremendous amount of clients that tell us, we hit these FFFL numbers, but this machine doesn't work right, or we can't put this installation in. Our environment's not quite right. Unfortunately, most of the time, they're finding this out after the fact. So what am I saying to a group of concrete guys?
It's be cautious with FFFL moving forward as industry 4.0 comes online in the logistics world. FFFL is really a statistical sampling of the floor. It doesn't necessarily cover every characteristic of the floor, but it is the way that we measure it here in the US. So.
It does still correlate. If you have a very high FFFL number, you may hit a lot of the criteria that you need to. However, you may not hit all of them. You can't just rest on your laurels and say that we have a good FFFL number. We're going to be able to hit the robotics environment that's necessary. It's required that we do a little bit more research. We're finding a lot of clients get themselves into trouble because they're picking up a spec building or they're
going with more traditional specs on FFFL only to come and find out the environmental information coming out of the robot provider is more stringent or different. Ways that this can be is that FFFL is just a sampling. During a free movement floor, we care about every direction, not just a couple of plus signs or hashtags or Xs on the floor the way we test FFFL. Instead, we're looking
for a much more continuous picture because the robots can move anywhere on the floor. Or we come back to an FMIN spec or a defined traffic floor where we need to understand exactly the wheel paths and exactly how flat the floor needs to be. In either one of these instances, FF and FL are not enough alone to ensure that the client will have the floor that they need to run their program.
Seth Tandett (04:24)
Yeah, let's, there's a couple things you mentioned that I want to make sure we define for folks. So you said a free movement floor. What is a free movement floor?
Derek Cressman (04:34)
Well, it's exactly what it sounds like. So a free movement floor is a floor where the robots can travel in any direction. It's an undefined traffic pattern. Most of the time from what we have seen in our experience on the floors, they're not moving in diagonals, but they are typically moving in a north south or an east west direction in a defined area within the building. We call those free movement floors because they can track anywhere.
Seth Tandett (04:56)
Okay, and then you briefly mentioned F-Men. Let's define that. So what would be an F-Men floor?
Derek Cressman (05:04)
So an F-min floor is more like a, we call them, a broader name is a defined traffic floor. And so in a defined traffic environment, the fork truck is restrained to certain aisle ways. Think about a very high pick warehouse, the forklift has to be on a very defined traffic and we will only analyze and correct the areas within that defined traffic. A lot of times these,
machines run on wire guides so they cannot deviate from their path, are locked on and can go. That's more of a defined traffic. FMIN is a very stringent spec. Coming out of Europe, there's a VDMA spec that's even more stringent. So these specs are very, very high tolerance and require a significant amount of layout and front-end work to make sure that the end result is a positive, high-efficiency result for the client.
Seth Tandett (05:49)
Yeah, so for folks that aren't familiar with measuring how we measure FF and FL, we typically use what they call a dipstick and it's a machine that you walk across the floor, kind of rolls across the floor, and usually you it over, 10 feet, right? 10 feet is usually minimum of 10. Yeah. So there's no...
Derek Cressman (06:04)
Minimum of 10 feet. Yeah, that's that's for levelness. Yep.
Seth Tandett (06:11)
I haven't seen, maybe you've seen, where they define where you got to take the measurement at. So they don't tell you, hey, you got to take your FF and FL in these areas. So it's kind of up to the contractor where they do that. And the third party, because typically a third party guy goes in there and does his measurement as well. I don't know if all can.
Do all, we do it, but do all contractors kind of self measure as well? you? Yeah.
Derek Cressman (06:44)
think a lot of the big guys that are working in these industrial
markets with us, a lot of those guys are out there walking their floors because they want to know that the testing agency is doing it right.
Seth Tandett (06:54)
Yeah. So that's what we're, I guess I'm trying to set the table for you, Derek, is that's how the floors are measured. And by, if the specifications call for that. So typically you'll have, if you look into specifications, they say, that you need a, this is your FF you got to hit. This is the FL you got to hit. And then, you know, right now the way, unless, have you seen it?
the measurement requirement defined a different way other than using a dipstick? Like have you seen them say, you got to use a, I don't know, a scanner? Do you have to use a 3D scanner? Have you seen that at all?
Derek Cressman (07:27)
Yeah, it really depends.
mean, you guys actually did a really nice job with Leo Zhang there from laser scanning in one of your previous podcasts. But yeah, there's multiple ways to kind of go at this problem.
For a free movement floor, yeah, a lot of times the best way to begin to look at that is a scanner because it gives you a good picture of the floor. The problem with the scanners is precision wise, we can't quite get down on what some of the robot manufacturers.
need. So there's some additional measures. A lot of times what happens is a tremendous amount of statistical work either by using a walking profiler such as a dipstick or a 1155 or what's known as a rolling profilograph which is basically a few dipsticks put together on wheels that analyzes the floor and gives you a topography of the floor.
Then it's all stitched together through a litany of math and you get a organized chart that begins to tell you which parts of the floor fall within the bandwidth and which do not. It really depends on the spec. That's free movement. In defined movement floors, the fastest, most easiest way is by far the rolling profilograph.
instrument. You can do it with the walking D meters but anybody that's ever done that knows that it is a very long and painful process and if you mess up halfway along the way it'll make you absolutely crazy.
Seth Tandett (08:51)
Yeah. And the other challenge too, what is, so the concrete contractor, third party guy that's doing the FF and FL measurements, they have a window of time to do it in. That's between 24 and 72 hours. So they can go over there and measure it in that window, hit their numbers. But what happens to the concrete after that, Derek?
Derek Cressman (09:13)
Well, here in the northeast it twists and turns and curls and carries on no matter how much we try. Everybody seems to experience some form of movement or sub-bass or issue, but concrete I feel like is a living breathing thing and it does twist and turn on us here.
Seth Tandett (09:29)
Yeah. So.
So like you said, hit your FFL numbers and that meets the spec. But what you're saying is due to the newer robotics and equipment that are used in these warehouses, that's not enough. ⁓ So what do you have to do to... I guess where does that spec come from?
Derek Cressman (09:47)
That's exactly right.
Seth Tandett (09:53)
that are, do the robotics manufacturers, do they give that to the contractor? Who do they give that information to and what does that look like?
Derek Cressman (10:03)
So that's one of the
trickiest parts and that's where we are trying to create some elbow room a little bit in the industry. So a lot of times these buildings are being built before anybody even knows which robotics package is going into it or maybe that.
That problem hasn't been solved for quite yet as land development's approved and we're beginning to build these buildings out. So we're going with what we know here in the states with an FFFL number. And that's not a bad way of doing things because if you push the FFFL numbers up, we know that the place and finish guys are gonna need to be paid more to take that risk. That makes perfect sense.
But the answer to who is creating these rules is each robot manufacturer. So when our clients sign up for whatever sophisticated automation system, ASRS system or AGV system that they want, it comes somewhere deep within the paperwork and environmental spec. And this environmental spec begins to dictate how that floor is going to interact with the fork truck. Sometimes our clients...
get it up front, sometimes they find out the hard way, unfortunately, that they didn't meet the spec. But each one's a little bit different. The robot manufacturers do a really nice job most of the time of knowing exactly what their systems can handle and cannot handle. It's a function of height, it's a function of speed of the robot, and it's a function of how tight the building is laid out. So each one's a little bit different.
But it is an important question to ask. Understanding the environment which their specific selection needs to run in is a critical piece of the puzzle as automation begins to take hold and Industry 4.0 comes into our logistics program in America.
Seth Tandett (11:37)
So you mentioned, I didn't know if you caught or yet you explained. So AGV is automated, I had to look this up, automated guided vehicles, right? And then, ⁓ did you say AMR?
Derek Cressman (11:49)
Yep. That's.
Yeah, well AMR is another piece of the puzzle in this. There's a hundred different acronyms and things like that, so I apologize. Yeah, and AMR is an autonomous mobile robot, I believe is the name for that. And then ASRS is automated storage and retrieval systems.
Seth Tandett (12:04)
huh.
Derek Cressman (12:10)
And these are all different varying types of robots that are beginning to find a foothold in large industrial buildings and e-commerce fulfillment centers throughout the country.
Seth Tandett (12:20)
Okay, and I assume.
These are all foreign manufacturers, is that correct? Is that correct, Steven?
Derek Cressman (12:27)
A significant
amount of the ones that we see are coming out of Europe. you know, it's anybody's guess. Anybody can make these things. We just, we adapt as we see them. Our job is to adapt the floor to whatever is put in front of us.
Seth Tandett (12:40)
So when you get these requirements from these robotic manufacturers, does it look like?
Derek Cressman (12:46)
Typically it comes in table form and it really depends going kind of a little bit of recall here whether or not you're going to free movement or to a
to an FMIN or VDMA spec. So in free movement, you're looking at a table typically with a series of criteria which correlate loosely to a flatness over a gauge, be it a meter, two meters, four meters or 10 meters, and then a level grid usually laid out over three meters.
And then you have a requirement of just how much gap under straight edge for lack of a better term you can have in this environment So that's how a free movement floor works But and then that can happen in any kind of direction as you're trying to carve out the problem on the floor in Defined movement that's typically classified by a number
Seth Tandett (13:22)
Yeah, we did an episode.
Derek Cressman (13:35)
You know in the F-min system it would just be an F-min 100 or an F-min 60 and you can peel back the onion on that a little bit further and say well How much is it in the transverse direction? Which is how much wobble does the forklift have left to right versus how much in the pitch direction longitudinally forward and backwards so there's a litany of information that you can begin with and then peel back to make sure that you're trying to get to the right place for the client
Seth Tandett (14:03)
So if you're part of a project team and you are building one of these facilities
what recommendations would you give them as far as making sure they're protecting themselves that, you there's no confusion on what the deliverable is. So if you're a concrete contractor and there's an NF number in there, is there a recommendation you would have to say, these are the things that you would look out for in a spec to make sure that one, that your
you're protecting yourself from future confusion. I guess also, there's, everyone's on the same page as far as what the deliverable looks like at the end. Because we were talking before, I guess, to fill everybody in. So I was part of a team that built one of these Amazon robotic distribution facilities.
And the specifications were, and the project team were all set up for a company like Derek's to come in and do what we would call the dry finishing. So there was an FL numbered for us to hit. We hit that, and then there already was money allocated to having Derek come in. But what Derek shared with me was,
not all of the companies out there are refined as Amazon and they understand that there's that second step for a dry finisher to come in after the concrete contractor delivers the, you know, delivers the FFFL per the spec. There's a bit more that has to happen for the robotics and the equipment to work.
So what should we be looking out for? Circle background, Derek, sorry.
Derek Cressman (15:39)
No problem. So yeah, I mean,
I think that's a really important piece and really a lot of it is setting good expectations. I think you hit the nail on the head.
I'm not sitting here advocating that we change the world. think that FF and FL is probably the way that the place and finish contractors are going to want to do this. that's fine. It's really setting the expectations upstream. We have a tremendous amount of end user clients that come in and like, well, I had an FFFL of a 75, 45 or pick a number. Of course we can put this robotics platform on and come to find out after the fact that
Things didn't really work out that way. And so it's really understanding what FF and FL are telling you. I think a perfectly good way to protect the concrete contracting community is still within FF and FL. As long as they understand, everybody understands, including the testing agency and the owner, what you are delivering.
Because ultimately when the owner comes in and their robotics package doesn't work that well and the environmental page doesn't really match up with the FF and FL that was delivered on the floor, that's when these more difficult conversations start. And that's when we come in and say, hey, give us a little bit of elbow room, is that the technical grinding service so that we can solve the problem together and get a floor that was a perfectly good floor and met spec in FF and FL. But now we can get
it to the environmental requirements of the robot which may or may not correlate with the FF and FL system. So it's really, there's not a lot of concrete contractor can do other than sign up for the specification and then make sure that the testing and acceptance is very well defined. The worst thing in the world is when you have an owner that's upset because it doesn't, their environmental is disconnected from the floor that was delivered to them.
And it's just making sure that there's open lines of communications. In the way we do construction here, a lot of times we're off and running prior to maybe they're making a selection of the package or maybe they don't know exactly what's going in the building. They're down to three different vendors for a robotics platform. Those three different vendors all have three different environmental criteria that may or may not correlate.
with the number so that it's getting the project team to understand there's a gray space in there that needs to be talked about. It can't just be swept under the rug because fixing the problem after the fact is extremely difficult.
Seth Tandett (18:02)
Yeah, so are we in the States, are we doing, I don't want to say something wrong, but are we doing something different than say Europe as far as how they address this? Are they doing it differently than we do?
Derek Cressman (18:14)
I think that they're, well, I guess the answer to that question is I don't think we're doing anything wrong. We just build very fast here. So with speed comes some potential agitation. Maybe the floor specs are already set and maybe the floor's already going in long before we know even who's going in the building, let alone what robot package they're bringing with them. So it's very hard to deliver a robot ready floor when you don't know what robot you're getting ready for.
In Europe, I think that they are a little bit more thoughtful in kind of what the end result is going to be and timing wise, what they are willing to allocate to see a project through. That's some of the feedback that we've been given by some of our European peers as we begin to ask questions on how they've surmounted some of the issues that we face from day to day.
Seth Tandett (19:00)
Is there any groups that you're aware of or maybe you're a part of that are addressing this in a, you know, like an ACI or something like that where this is, you know, I guess someone's documenting this and contractors can point to that or check, use it as a guide to make sure they're, you know, going at this the right way?
Derek Cressman (19:27)
think there's a lot of conversations about changing or beginning to publish the documents, something like that. ⁓ I don't know that anybody has grabbed a hold of the whole idea yet and ran with it, but I've heard in certain circles around ACI, the idea has been brought up, but nobody's grabbed the whole thing and put their arms around it because...
Seth Tandett (19:35)
Yeah.
Derek Cressman (19:49)
Every environmental specs seems to be a little bit different. They're all close, but different. And so the other thing that's really interesting about as our industry, know, steadfast, we do things the way we do them meets tech industry and constant change. It's very hard to keep up with their specs because they're improving these robots daily. We're on some floors where the challenge has been
you know, fix the floor as best as you can within this budget and simultaneously look at the robot contractor and say, you make that robot work with this floor, you know, the best that we can deliver it. So there's such an evolution. We're all learning so fast. It's really hard to wrap your arms around it and say, well, these are the hard and fast rules because there is this very large gray area.
Seth Tandett (20:23)
Mm. Yeah.
Yeah. Yeah, I was thinking when you were saying that, that, you know, the lot of speculative warehouses that were built over the last handful of years, I could see where that's a problem, where someone goes, yeah, I'll buy that building and I'm going to, you know, either be a warehouse or I'm going to manufacture something in there and you plan on using these certain robots that...
I wonder how often people actually consider the floor flatness or the condition of the floor before they actually make that purchase.
Derek Cressman (21:05)
But a
very interesting staff that some of our marketing team dug up through some of our conversations in the industry is that 40 % of automation failures actually begin with the floor.
So I guess that begins to answer some of that question. We do a tremendous amount of what the industry seems to be calling brownfield site rehab. So I'm living in a warehouse. Maybe I can't find employees. And so we're going to switch to some form of automation. We do a ton of repair, not just technical grinding, but a ton of repair work to get these facilities ready for the robots to come in. a lot of these things are often overlooked and I can give some
some pretty wild examples of things that we've kind of run across through the years. We had one experience with a very large bakery client that couldn't find employees, bought a awesome automation system, and ran it. And...
The problem that they were having is at the joints, they were curled and then beginning to erode away. They were breaking these custom bearings within the forklift. They were something to the tune of $12,000 a piece and they were breaking so quickly that they took a fleet of, I believe, 30 machines and had it down to 12 because they were cannibalizing all the parts. In reality, the floor repair only took...
maybe a week's worth of time to get these things fixed. And they wound up running through the better part of a global supply of these specialized glass bearings at $12,000 a pop. So it is often overlooked and you're like, you kind of look at it and say, well, that was a solvable problem. And in that regard, we've had other experiences where very, very large
Seth Tandett (22:33)
Ugh.
Derek Cressman (22:46)
800 900 thousand square foot robotics machines have been put in only to have a utilization of around 30 % because of the condition of the warehouse. We go in, we do some work, 30 % becomes 99%, all floor related. So the success of their overall implementation does start with the floor. The hard part is getting that little bit of elbow room in the industry.
before the robots start to run and break.
Seth Tandett (23:12)
Yeah, yeah, this was all this is all good stuff. Derek, the one question I have for you on a new build. What is the ideal timing for you all to come in and do your work?
Derek Cressman (23:24)
So I think for me, we try to say, does the installer of the automation system come in? And then we try to back our schedule start data from that.
because I want to be able to say that we delivered exactly what they need the day that they put their boots on the ground. Because we are all dealing with so much in the chain of construction, right? Especially across the country, it's hard to say what each condition will be. Texas has expansive soils. We have curl up here in the Northeast. You guys have your trials and tribulations with cement. So we try.
to back up from when the boots will be on the ground from the automation provider and do our work then. That gives the concrete as much time as it can to do whatever it is it's going to do. Gives us some construction traffic, some ride traffic, some loading, things like that so that we can better predict what we'll need to do to deliver the right floor.
Seth Tandett (24:15)
Yeah.
So is there a time when you're doing that back schedule, I guess, and you're working yourself back and you're like, whoa, that's too close to the time we poured concrete.
Derek Cressman (24:26)
all the time. Because that's the way the world works, right? It's a minimum of 28 days really for us before we know that the concrete's cured out. mean, that's just been an industry norm. It doesn't make a ton of sense. And quite frankly, it's...
It's more difficult to grind and be productive on those greener floors. So we do try to take the position that it's minimum 28 days, but wait as long as you can. Let's see what this thing is going to do.
Seth Tandett (24:49)
Yeah. Well, this was great, Derek. I appreciate you coming on the show today. I know we saved somebody oodles of money today if they listen to this episode. Yeah. If folks want to reach out to you and, you know, ask for some help, what's the best way to reach out to you?
Derek Cressman (24:58)
I hope so.
Best way is you can check out our website it's www.durablesurfaces.com or you can reach me on my email it's derek at durable surfaces dot com
Seth Tandett (25:18)
Good deal. Thank you, Derek. Appreciate you coming on the show today and folks until next time. Let's keep it concrete.
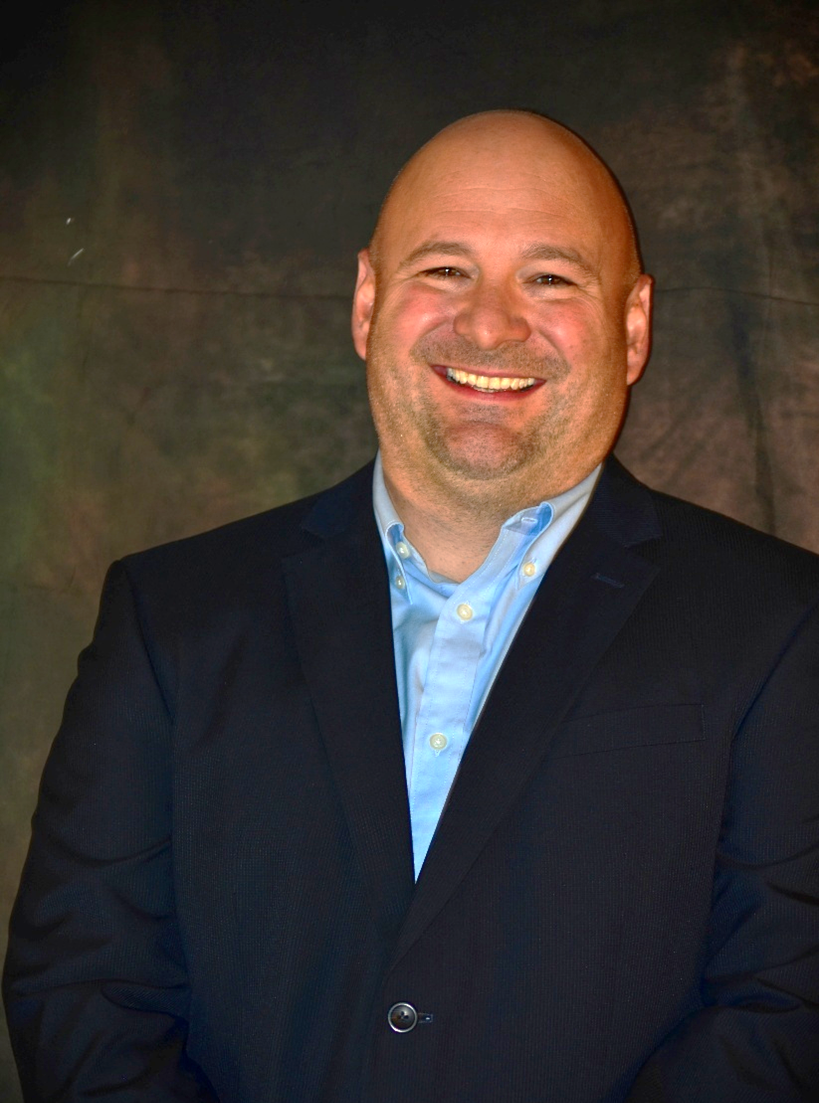
Derek Cressman
President
I have worked in concrete for about 30 years. Specifically the construction of large industrial buildings for the last 20. Since joining Durable 8 years ago we have embarked on a journey of taking existing buildings and making them robot ready for the supply and logistics of tomorrow. This involves a tremendous amount of work around the topic of flatness and levelness.