EP #122: How to Eliminate Concrete Cracks —Is Shrinkage Compensating Concrete Worth the Money?
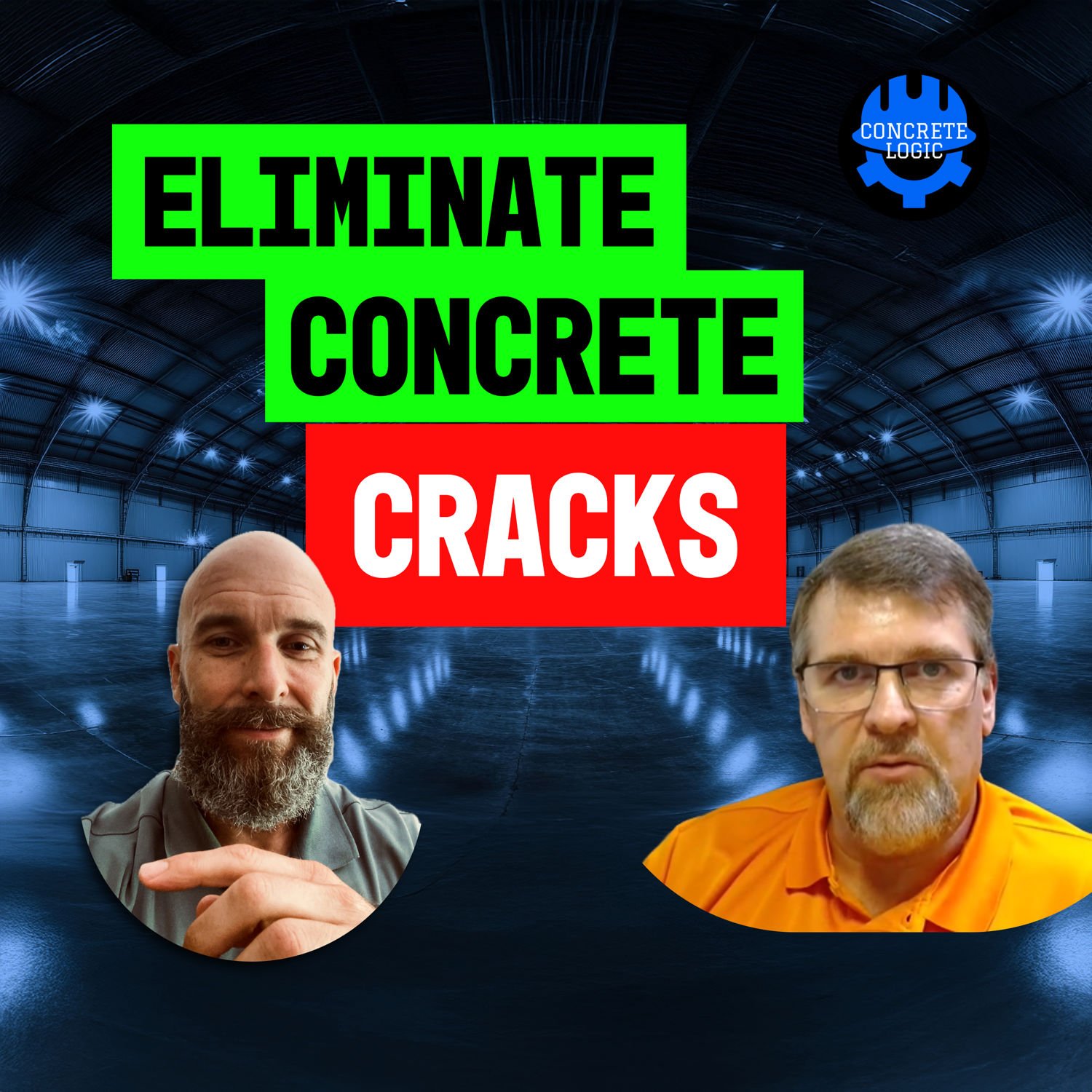
Are concrete cracks draining your profits and ruining your reputation?
In this eye-opening episode of the Concrete Logic Podcast, host Seth Tandett sits down with shrinkage compensating concrete expert Lee Thrasher. They reveal how this innovative material eliminates cracking, significantly improves long-term durability, and boosts your project’s profitability. Discover why industry leaders are switching to shrinkage compensating concrete, how it compares with traditional mixes, and why proper water curing is critical for success. Plus, find out how new blended cements are transforming the industry’s future.
What You'll Learn in this episode:
- How could shrinkage compensating concrete save you thousands in maintenance costs?
- Why does shrinkage compensating concrete virtually eliminate cracking compared to traditional concrete?
- What's the critical secret behind water curing shrinkage compensating concrete?
- Can shrinkage compensating concrete be effectively used in structures beyond slabs?
- How can investing in shrinkage compensating concrete lower your long-term project expenses?
- Why are blended cements becoming the go-to solution for the concrete industry's sustainability goals?
- What essential testing and quality checks ensure your concrete performance stays consistent despite changing materials?
- How does shrinkage compensating concrete truly work to offset drying shrinkage?
- Could adopting shrinkage compensating concrete streamline your construction schedule and reduce delays?
- What new developments in shrinkage compensating concrete will shape the future of your concrete projects?
CHAPTERS:
00:00 Introduction to Shrinkage Compensating Concrete
01:37 Understanding Shrinkage Compensating Concrete
10:07 Challenges Addressed by Shrinkage Compensating Concrete
13:51 Water Curing and Its Importance
16:46 Impact on Construction Schedule and Costs
21:24 Cost Considerations of Shrinkage Compensating Concrete
25:45 Replacement Percentages and Material Testing
31:00 Future of Blended Cements and Sustainability
35:17 Embracing Change in the Concrete Industry
LISTEN NOW – Every concrete contractor, architect, engineer and ready-mix concrete producer needs to hear this one!
Guest: Lee Thrasher
Email: lthrasher@ctscement.com
Company: CTS Cement
Website: ctscement.com
=============================
Take Your Knowledge Further – Join Concrete Logic Academy!
Gain exclusive access to expert video courses, live Q&A, and cutting-edge industry insights. Earn Professional Development Hours (PDHs) and elevate your expertise!
Learn More: https://www.concretelogicacademy.com
Support the Podcast – Be Part of the Concrete Revolution!
Donate: https://www.concretelogicpodcast.com
Become a producer & get recognized on our next episode!
=============================
Producer: Jodi Tandett
Music by: Mike Dunton
Instagram: @Mike_Dunton
Stay Connected & Watch More!
Host: Seth Tandett
Email: seth@concretelogicpodcast.com
LinkedIn: https://www.linkedin.com/in/seth-tandett/
YouTube Channel: https://www.youtube.com/@concretelogicpodcast
Podcast Website: https://www.concretelogicpodcast.com
LIKE, SUBSCRIBE, COMMENT & SHARE for more expert concrete insights!
00:33 - Introduction to Shrinkage Compensating Concrete
02:10 - Understanding Shrinkage Compensating Concrete
10:40 - Challenges Addressed by Shrinkage Compensating Concrete
14:24 - Water Curing and Its Importance
17:19 - Impact on Construction Schedule and Costs
21:57 - Cost Considerations of Shrinkage Compensating Concrete
26:18 - Replacement Percentages and Material Testing
31:33 - Future of Blended Cements and Sustainability
35:50 - Embracing Change in the Concrete Industry LISTEN NOW – Every concrete contractor, architect,…
Seth Tandett (00:04.019)
And welcome to another episode of the Concrete Logic Podcast. And today I have Lee Thrasher with me. He is a representative for, is it CTS? All right. And he is our resident expert today on shrinkage compensating concrete. So we're going to, there's four things that we're going to teach you today. What?
Lee Thrasher (00:16.878)
CT estimate,
Seth Tandett (00:32.803)
exactly is shrinkage compensating concrete and how does it differ from traditional concrete. We're also going to explain some of the common challenges shrinkage compensating concrete helps address in terms of cracking and long-term durability. We're going to cover how ReadyMix producers and contractors incorporating shrinkage compensating concrete into their projects today and what's the impact on construction timelines and cost.
And lastly, if we don't run out of time, we're going to look ahead and see how shrinkage compensating concrete is evolving as a material and if there's any exciting developments on the horizon. All right. And with that, you can tell us a little bit more about yourself or we can roll right into explaining what is shrinkage compensating concrete.
Lee Thrasher (01:28.046)
I certainly love talking about concrete more than myself. So let's just roll right into the concrete part. That's all right with you.
Seth Tandett (01:32.519)
That sounds good. Yes, sir.
So yeah, so what our first our first thing here is what exactly is shrinkage compensating concrete and how does it differ from traditional concrete in terms of performance and durability?
Lee Thrasher (01:50.254)
That's a great place to start because that's often.
the conversation we get into because folks when they hear shrinkage or drying shrinkage or overcoming those things, a lot of them go right to shrinkage reduction because shrinkage reducing admixtures is what a lot of people are more familiar with simply from the brand recognition, name recognition that's out there and more commonly used. However, shrinkage compensating concrete does exactly what it says it's going to do, same as those do exactly what they say they're going to do.
shrinkage. Shrinkage compensating is typically done with an expansive component on the front end where the initial volume of the concrete
expands, laboratory expansion at the early age to offset that eventual drying shrinkage. Concrete is always going to have some drying shrinkage element to it. What we do with shrinkage compensating is we just make sure you have a higher initial volume that you start with so that you end up at a little bit of residual expansion or net zero volume change.
Seth Tandett (02:56.673)
you make that sound so easy, Lee. I mean, how is that done?
Lee Thrasher (02:59.766)
you
Lee Thrasher (03:03.818)
Yeah, it is easy. It's the best easy button for long-term durability and dimensional stability you'll ever get, you know. But, you know, some things that are, you know, out there, you can find an ACI-223 and it talks about several different materials that are used that are expensive materials.
At CTS Cement, we're really proud and we obviously are known for Type K and Type K cement. And what we use today is the component product, component of the K. And all of that is in honor of Professor Klein.
with a K who worked with our company founder, Ed Rice, back in the 60s to develop what is known today as type K cements. There were expansive things that are out there in that chemistry, but it was an adjustment to the chemistry of typical Portland cement so that you would have that early age expansion. Typical blended in Portland cements today, they are at their highest volume actually when they're in that truck or when they're in their fresh properties. As they lose that water, they are going to shrink.
happens and that chemical reaction takes place, it consumes volume and it's going to shrink. So Ed Rice wanted to overcome that. He wanted to find a way to make cement better and have a better material to work with. So he worked with the Presser Klein and they created type K cement and went on to do a lot of other things with calcium sulfoluminate cements. We've got several different brands under CTS banner today. Excuse me. But the component is what we use today or type K cement, one. Those are two different things.
we provide today to provide shrinkage compensating concrete. So the material is used as a cement replacement for Portland, whether that's replacing all of the Portland in a mix with a type K cement that meets ASTM C845.
Lee Thrasher (05:01.098)
Or we do it with the component of the material like you would use with any other SCM dry powder. Works to a silo, goes in a percentage replacement. The type K is used at a 15 to 18 % or so give or take replacement there that we're replacing with that local Portland so that we're only manufacturing and shipping across great distances the expensive material and that will allow that
local mixture to then become the type K shrinkage compensating mixture that expands at that early age. And so the general process is it'll expand in that early age, typically somewhere between 0.04 and 0.08 percent, just to offset that drying shrinkage. Like I said, it'll happen in the first...
two or three days under wet care. We typically wet care for seven days and once you remove the wet care, then that material is allowed to go through the typical drying shrinkage and get back down to net zero. And then unlike a SRA,
Once it reaches that stability, it's stable for the life of the structure, for the life of the concrete. It does not undergo any other volume change characteristics other than typical thermal dynamics. That's a mouthful.
Seth Tandett (06:27.451)
Yeah. So it's an SCM. So this is being done at the Ready Mix Producer at their facility, right? That's where the mix...
Lee Thrasher (06:39.278)
Yeah, you can. That kind of gets into, like you mentioned, how's it used today with contractor ready mix producer. Obviously ready mix producers like to have the majority of that quality assurance and quality control at the plant. So they are running it through their plant process in the truck.
the material shows that it's ready to use. There's plenty of the proprietary systems that we talked about, or the guys that are doing the slab design, they're providing their version, their brand, their deliverable of that high-performance floor, and a lot of those projects they will dose on-site.
whether that's adding the raw material, putting it into a slurry, or they have a, some of them have pre-mixed bags and a couple different things that go with it to put it in at the job site from a base mix design, mix it up a little bit there and then they're off to the races in that method of delivery. So it's really either or, whatever's best for the project. We'll do whichever way is best for the project as a whole.
Seth Tandett (07:46.935)
Okay. But not at the cement manufacturing facility, right?
Lee Thrasher (07:56.716)
That's only if we're making a type K cement.
Seth Tandett (07:59.579)
that's where you make, yeah, you produce that, but you're not like getting involved where after the clinker's made and then they're doing grinding and mixing in that second part of making cement.
Lee Thrasher (08:14.946)
Well that, we are a cementitious product so we are made at the mill. So it is a, yeah, Baleitic calcium sulfoluminate cement. I need a sip of water if I'm gonna say that again.
Seth Tandett (08:20.037)
Okay.
Seth Tandett (08:25.071)
Okay. Yeah. All right. Well,
Lee Thrasher (08:29.964)
Yeah, so where you've got Portland cement, we are a calcium sulfoaluminate cement. So when it's made at the mill, think of it this way. This is the way Susan Foster explains it. I love it because it really made sense to me. If you think of that clinker material that we make as a cocoa bean,
Seth Tandett (08:34.234)
Okay.
Lee Thrasher (08:49.432)
Well then if you grind and process that cocoa bean in one manner, you get hot chocolate powder, right? And you just simply add water and you've got instant hot chocolate. That's our rapid set version of calcium sulfaluminate cement. So it's ready to go in the bag. It's a rapid set, rapid repair. We say mix with water and land a plane in an hour. We get three and 4,000 plus strengths very, very quickly.
The other way you take that same cocoa bean and grind it and process it, you have the chocolate powder like you use to make a cake. And so you need the other ingredients of that cake and time and heat in an oven to make the final product. It's still a great taste of chocolate, right? It's just two different products, ultimately, with the same raw ingredient. So at the meal, we're making that raw clinker.
Seth Tandett (09:46.379)
it all right how many well I think we could go down a rabbit hole there but I'm gonna try to keep us on task all right so let's go to can you explain some of the common challenges shrinkage compensating concrete helps address particularly in terms of cracking and long-term durability
Lee Thrasher (09:53.368)
Probably so. Yeah.
Lee Thrasher (10:07.252)
Absolutely. So we can virtually eliminate dry and shrinkage cracking. I mean, we are taking care of that expansion so that we're offsetting those forces. It still happens. And so if you don't engineer and design it properly, and we do say it's engineered expansion, it's just not running wild. There's a lot that goes into it and it's definitely controlled and we work very...
diligently to make sure on the testing on the front end that we've got that correct so that we're exhausting that reaction so you stay above net zero but if it's not done correctly you can go below net zero and you will still have drying shrinkage that will that will occur but other than that
Our goal is to eliminate drying shrinkage completely. You still have to protect yourself in the process in the plastic state against plastic shrinkage cracking. And of course, if you've got things like sediment and other elements that can crack concrete, we're not going to somehow modify your subgrade.
Seth Tandett (11:08.314)
Right.
Lee Thrasher (11:08.716)
with fresh concrete. But other than that, you can have dimensionally stable. We follow ACI 223 guidelines. So we're typically starting our joint spacing at 150 feet, but we've done projects. was just looking at one in history here in Atlanta, we did 340 feet on exterior paving and some of the joint spacing on that.
We've done plenty of projects where we're using a three to one ratio. We've got plenty on the ground that are little bit better than that with just some longitudinal axis reinforcing. Added in to control that a little bit better against the curl. But in most applications, you don't have trying shrinkage cracking. You don't have curl. Creep is virtually eliminated as well.
So outside those environmental conditions after the concrete's in place, the forces of the concrete itself are...
managed and engineered right out of there. So obviously you have fewer joints, less maintenance. You've got, you don't have the curl, so you don't have that differential movement a lot of times that you would get that would increase settlement and create cracking and things like that. So as long as the best practices are followed and everything's isolated and let's it do its thing, it's very stable for the life of that concrete. And because we're handling expansion by creating
creating etronite crystals in that void space, the permeability and absorption is virtually nothing. We make a very dense material after that initial curing period.
Lee Thrasher (12:50.208)
So things that would typically attack and degrade that concrete, know, the vast majority of those things happen through permeability and happen through penetration. Water carries a lot of bad things, know, chlorides and sulfates and acids and things that are all in liquid state that get down and permeate into the concrete. Well, we don't let that happen either. So we're providing a great, great finished surface. a of contractors that are out there that do shrink concrete for industrial floors, manufacturing,
Seth Tandett (12:58.79)
Yeah.
Lee Thrasher (13:20.112)
storage, things like that. And even in areas where we're the basin slab in a sludge basin, or we're doing containment walls for liquid containment, things like that, you see a much better life cycle cost because you have less maintenance and you have less openings and penetration points as far as joints go in that initial construction. So you get a great offset of the cost in that.
Seth Tandett (13:46.551)
Is water cure just mandatory to make it work?
Lee Thrasher (13:51.374)
Well, water curing is always the best thing for concrete anyway. You know, certainly in areas where it's cold climates and things like that are elevated, it becomes, you know, a constructability thing that we really got to look into and address. But there's great products out there today with some of the blankets and things that can go down that absorb that water on one end and maintain that impermeable surface on the other side. The biggest thing is
Seth Tandett (13:53.895)
Yeah.
Lee Thrasher (14:19.714)
Typically expansive materials consume much more water than typical Portland cement does or blended cements do. We're a better utilization of water because we're filling that void space with more product, more things that are reactive. So it needs every bit of that mixed design water. Not so much as it used to be in the past where you really had to increase the water cement ratio and you really had to watch it because the materials would really, really significantly drive water to
If you look up a lot of literature from years gone back, you'll see that. But with today's component materials, that's very, very manageable and very much under normal conditions. So what we got to do is just make sure we have that 100 % relative humidity so that the engineered side of the process, of the design criteria to make sure you get what you're expecting happens. Having 100 % relative humidity guaranteed on all aspects of that surface
edge to edge, corner to corner, is the only way you're going to get that assurance nine times out of ten. And we're working on things, that's, you know, but it's down the road.
Seth Tandett (15:31.345)
Yeah, you're saying working on things that would not require the wet carrying short.
Lee Thrasher (15:37.548)
Or shorten the timeline. 223 right now is seven days and there's plenty of folks doing some research and trying to figure out with newer materials that are on the market today, how can a combination of things or how can things work to try and reduce that seven day timeline or that are more appropriate in cold climates where you're going to have maybe great for pleasing the slab that day, but you're going to get down to freezing overnight. And that's certainly some safety issues and things.
like that. had a big old frozen slab. So trying to figure out the best way to maintain a wet care environment without a flooded seven-day slab is on the horizon, I think, down the road.
Seth Tandett (16:22.983)
So that's perfect. It kind of rolls us into the next item was, you know, talking about construction schedule and cost and how this impacts that. So first of all, it sounds like you got a plan for a seven day wet cure. Is there any, other things that you got to consider?
Lee Thrasher (16:46.563)
So who?
Whoever your supplier is, and we certainly do it, we get involved early on our project to coordinate between the ready mix producer, the place and finish contractor, and then if it's a different entity, that general contractor that has the site control and really get everybody on the same page as to what that process looks like. So we're huge proponents of pre-construction meetings as well as pre-pore meetings. And at pre-construction, we're going to be reviewing the design and details and layout of that joint layout.
Duh.
trend here lately has been to be able to, just about every project has the ability to go jointless if the producer can provide the volume of concrete. So whether we're sticking with the slab thickness or we're thinning the slab, a lot of times that square footage falls within the joint spacing we can accommodate there. Might have to have a single saw cut or maybe a pour through armor joint or something like that. But in a lot of cases, we're utilizing the placement schedule
as the joint layout. So you certainly have the time of once you get the wet care down, you're done. The guys aren't there staying to saw cut and things like that. And then depending on how you do your panel layouts and things, we can typically, if you've got a larger project that may have, for example, one I talked about last week with a friend of mine, was 16 placements and with our schedule, they could cut it down to 12. So being able to reduce the overall placement time.
Lee Thrasher (18:20.552)
In most cases, we can find a way to offset the delay you might have with the wet cure. And really, if you've got multiple placements, you're kind of offsetting those anyway. You want to have at least a 72-hour window before you place fresh concrete against freshly placed, know, something that was a recent slab that was placed. You're going to isolate it if it's existing concrete, like an expansion of a building or something like that.
You don't checkerboard it necessarily. You just stagger the placements. We work with folks to do those different layouts to make sure it's going to fit.
One of the areas where we're seeing certainly an increase in shrink-comp concrete is where you've got the high rack systems or automated systems and things like that. And that joint placement becomes a lot more critical. we can work, especially being able to do a different aspect ratio, we can work to kind of shift those elements around, move it in blocks and squares, rectangles, to really fit best for what those travel miles need to be, what that pathway for the automation equipment needs to be and things
like that. So all those elements do play into just helping the overall constructability for sure.
Seth Tandett (19:36.027)
Yeah, and it would, I would imagine it helps with the FFFL numbers as well. Is it easier for the guys to finish?
Lee Thrasher (19:50.316)
I to say what I want to say in today's world, absolutely. The concrete that I've seen lately is some of the best and the creamiest I've seen. I don't know if that's a result of, it just makes really good concrete and folks are struggling with concrete that's not the same as what it used to be. So they're having to already adjust.
Seth Tandett (19:55.461)
huh.
Lee Thrasher (20:14.99)
But just the nature of the way shrink concrete works, is a very high quality material.
your everyday run-of-the-mill combination of powders that are out there. So they do see a better performance and we can we can do a lot to help with giving a predictable set time. You typically have a less bleed
with shrink comp concrete than regular Portland mixers. Oftentimes it's just a nice sheen. You really don't get bleed because we're consuming that mixed water like I said. So a lot of guys that have done it really, really enjoy finishing shrink comp concrete compared to the rest of the building for sure.
Seth Tandett (21:09.019)
Yeah, I want to go back to talking about the amount that you replace of today's cement versus what you guys did before. So just put a mental note there. But I want to make sure we address the cost of this, know, compensating, shrinkage compensating concrete versus traditional concrete. I imagine it's a little bit more costly.
Lee Thrasher (21:24.92)
Mm-hmm.
Seth Tandett (21:39.151)
And, but these are, these are specialty floors that you're working on, heavy industrial manufacturing. So these are clients that need a high, I don't want to say high dollar, but a high value, high value floor. Is that, is that right?
Lee Thrasher (21:55.006)
High value. High performance. Yeah, high performance, value for sure. I like to tell people, you know, it's one of those things where when we get the phone call, somebody just making a general inquiry.
we can figure out real quick, you either need it or you don't. If you don't need it, then put the work on us to justify it and show you how it can work. Because you can actually apply shrinkage compensating concrete in a multitude of building elements, not just slabs. That's the world where most of it lives today and what people know it. A lot of that's due to the proprietary branded systems that are out there and the nature of those high performance floors.
especially things like cold storage and ASRS and high racks and things like that, you need a high-performance floor and a high-performance contractor to do that kind of work. The premium itself is sticker shock to some folks, but people who are familiar with high performance and looking at it in the holistic standpoint of using less reinforcement or being able to pick and choose which reinforcement works best.
for you. Having that impact on the construction schedule, possibly being able to thin the element because it can carry more load. Reduction of those joints. can find that if you're starting from a moderately extended joint system, or especially if you're starting from a high shrinkage reduction mixture, we're going to be cost competitive every time because you can really push those elements out there and you're dealing with folks that
to kind of understand that world. If you're going for just a traditional, you know, seven inch unreinforced concrete slab, and you're going to look at making that shrink top, that's a much heavier lift. It can be done, but you're going to have to have an owner that's going to maintain that building and want to look at that life cycle, you know, long-term to cost and factor in the drastically reduced maintenance. Same thing on anything that's in containment or pavements or bridge decks or things like that. You're going to
Lee Thrasher (24:10.402)
have to be willing to kind of look a little further than just what's my cost per yard because the cost per yard is is not your normal upcharge but it's certainly worth it and can certainly bring the value to that structure you know if you don't have to replace the concrete for centuries instead of years you're in pretty good shape and a lot of times where someone's going to consider shrink comp concrete they are the owner you know they're the ones that are going to be required to maintain it and so it
does make a lot of sense and we have a lot of success in having that conversation because we're starting from a point above just normal everyday concrete.
Seth Tandett (24:48.763)
Yeah, yeah, this, I mean, this, we talked a little bit about on the last episode, which would be episode 121 with Derek Cressman from Durable Surfaces. We talked about robotics and these automated, automation machines that require, you know, these high value floors.
So if you haven't listened to that episode yet, make sure you go back and listen to that because this ties in with Lee's episode here. So going back to what I told you to remember is we talked a little bit about, well, you mentioned a little bit about the powder of today. Have you seen a change between what
you all have done in the past as far as the replacement percentages. I think earlier you said you're doing a 15 to 18 % replacement.
Lee Thrasher (25:52.674)
Yeah. Yeah.
Yeah, yeah, and that's, that's what that's on the type K, the other.
A few of the other types that are covered in our 223 might have a little bit different percentage replacement. I would say as a whole, kind of in the industry, you might find it between maybe five and 30%, give or take. That's actually a range we're talking about now. We've got actually an ASTM standard on our proposal for the component materials that go in to have our own spec. But our window is that typical 1518. Our process is always
been, we'll get the producer materials from that local region into our lab and we'll run a battery of tests on the front end to determine what is that, you know, potentially against that dry and shrinkage and are we making sure we're hitting our targets because we've got, you know, we want to stay within all those guidelines. We want to have that engineered expansion and controlled volume change. So we're looking at that on the front end as we get different materials in from different parts of the country and a lot of those primary
know, Portland or blended cement sources are changing. We're having to...
Lee Thrasher (27:06.274)
pay a little bit closer attention to that in some regions. I had a project recently where we decided to run the test a second time, just to make sure that we had it right, because we wanted to make sure everybody had the quality assurance and felt good about the results in that process. in some areas we've seen where we've been able to go, actually go and use below our target dosage. Our particular...
baseline has been relatively unchanged for a while. We're evaluating that now to see whether you've got a 1P, a 1S, 1T or 1L, is that baseline gonna hold true across all those different types. So we're really excited about seeing where that can land for us going forward. But each and every time we're still gonna do that testing up front of that local materials because concrete is always has been, always will be a regional material, right? And as you're seeing an increase in variability
mill to mill, it's even more so. It's just reinforcing that fact. So, whereas a lot of people are having to go back and refresh their memory of how to evaluate cementitious powders because they've just been spoiled as I was for many years, being predictable without having to run the test because it was just so consistent. Any change brings about a...
invigoration of knowledge and having to go back and relook at things. So we're in that process just like everybody else is. But we're not seeing anything that's a drastic change from being like we got to go rewrite standards or anything as far as what our work is. So it might tweak a little bit, you know, where we might have used 15 % before we might have to go 17 or where we use 17 % before we might be able to get away with 15 now. But we're doing the test on the front end. That's the biggest thing, which is good for, you know, anybody in the concrete business. If you're
to change a powder test it test it ahead of time and test it as it goes through changes test it test it test it because it's going to change I guarantee you
Seth Tandett (29:03.451)
Yeah, yeah. I wonder, it's staying the obvious, but I wonder how often that actually happens.
Lee Thrasher (29:15.64)
Which part of that change in patterns? Testing.
Seth Tandett (29:17.633)
No, no, no. We know change is constant. I was talking about testing. We've talked about that on the podcast, testing your powder.
Lee Thrasher (29:24.214)
Yeah, most of the producers we work with have solid technical teams. And that's the vast majority of my background is being on the technical side of Ready Mixed Concrete. And so I may be biased because I love those guys. I love Ready Mixed Concrete.
think it's the greatest building material ever invented in the history of mankind, quite honestly. And that's not to say there's anything wrong with precast pre-stress or manufactured concrete products or anything like that. It's just, I think the time and the effort, knowledge, skill that goes into running successfully or ready mix operation decade after decade takes a lot of technical knowledge. It takes a lot of market knowledge and material knowledge because it's going to constantly change. So to take a imperfect,
adjustments in raw materials and consistently make a product that performs under all the different construction elements you put it under in ready-mix cast in place concrete. It's truly amazing if you think of it from that standpoint, you know, it really is. So I think a lot of those guys are getting really good at keeping tabs on their material and the ones that weren't and got bit lately are
revamping and adjusting and getting a whole lot better at doing more testing in-house beforehand. Or they should be. If they're not, if you're listening to this and you're not and you're one of those guys, adjust. Get ready.
Seth Tandett (30:47.877)
Yeah. Yeah. Well, that.
Seth Tandett (30:57.489)
Yeah, you're playing with fire right now. Yeah. Well, that was perfect. I wanted to hit on blended cements, so you already talked about that. So that's kind of the future, right? That's what we're getting into. And it sounds like you all are already doing testing with blended cements.
Lee Thrasher (31:00.3)
Yeah.
Lee Thrasher (31:15.79)
Yeah, yeah. And it's a lot of fun for me coming from the background I did and seeing it on liner side because when you look at things other than what that ready mix producer puts in their primary silo, whether that's a Portland cement or a blended cement, everything else brings its own unique characteristics to the game, right? And the fact that kind of like Slag, we are also a cementitious product.
we can kind of elevate that a little bit. we're looking, you know, that's why when you are asking me about, you know, that contracting the properties and finishability and getting their FFFL numbers, you know, I'm a huge fan of our product. Just like I'm a huge fan of slag. I like things that are cementitious and I don't have anything against ash. I've used them a lot. I love them. Even the, you know, calcine materials out there or, you know, medica aolin or I've played around with, you know, rice husk ash in the past.
and the ground glass pozzolans and things like that. There's a lot of great pozzolans out there as well. So it's a real dynamic time, not just from the Portland side, but also the SCM side. There's so many different combinations you can look at now. Having that solid technical team, great vendor partners, the ability to look at things in house for a ready mix producer is critical going forward. It's always been very, very important, but it's critical going forward because their customer
are putting more pressure on them just because of the buzz in the marketplace to have a predictable material. And that's always the challenge, keeping it predictable with those changes in raw ingredients. So the fact that you've got...
really high performance products you can put in those silos to compliment that blended material. I just think you're going to see so much advancement in a producer's understanding of how to best put those things together. It's going to be a lot of fun to be in that side of the business. Whereas most people looking from the outside in would say, you know, they don't even want to talk about powders because of pain of transition from one to the other. I look at it as a fantastic opportunity because there's things that
Lee Thrasher (33:26.404)
that need solutions out there that are not our typical problems. This is kind of like a new world we're entering into and you got a lot of options out there and we certainly want to be one of them. And I think we certainly can be because we've just got that inherent very high performance characteristics in our base material and our base product. And it's half the in typical comparison, half of the GWP impact of what you're putting in that blend.
blended cement. you know, we've been a highly sustainable material ever since the inception of the product back in the 60s and 70s. Just never knew to count it, you know. But go back and doing the math, our guys put together our EPD and they're like, wow, this is pretty awesome, you know. So we're in the mid to low fours and getting thinking about getting better all the time as far as our units of global warming potential.
Seth Tandett (34:21.349)
Yeah. Yeah. That's a whole other episode we can, we can talk about. I love your attitude about what's going on right now. Some people I get on the podcast, they, you know, they, the, the, the change that we're going through right now, they, they're just, they're negative on it. and it, it really, I think it's, you know, your personal beliefs on the whole, the carbon reduction, the global warming potential and all that. You kind of have to
set that aside and just embrace what's going on right now. I put it in a, I think in our newsletter last weekend when I sent it out, I said, no matter what side of that fence you're on, you gotta acknowledge it's an exciting time in concrete. There's a lot of change going on and it's gonna be interesting, certainly what concrete's gonna look like in the next five to 10 years.
Lee Thrasher (35:17.902)
Absolutely. It's going to continue to change. What we've seen in the last year to 18-24 months is just the tip of the iceberg in my opinion. And you're right, I think, and it's probably just because of
my history and background in some years of being a field technician and being on the technical side of ReadyMix, coming up to the business, I learned you got to embrace the pain, you got to embrace the hurt, man, because a problem is just an opportunity if you look at it correctly. And you're right, your own personal faith and approach and belief to everyday life can kind of help you navigate the world of today with social media and digitization.
AI and everything out there, you gotta keep perspective. Local, and you hear a lot of people talk about that as far as keep it local, keep it real. Well, that's concrete, right? It is a local business and you have opportunities every different city, every different place, every different job you go. You can look at it as there's just another complaint, you can let it wear you down. And too many guys, especially, we were talking earlier about the testing side of things. And that's the difference in approach we're taking there.
trying to be positive and do something about it versus, you know, amplifying the complaint. We want to do the same thing in my CTS world and for our customers and those readiness guys that I love and appreciate so much and understand that there's going to be significant challenges and how can you help? You know, don't want to sit around the pot or, in the lab in the morning and just have a 20 or 30 minute gripe session over, you know, things that are outside of our control. All right, you know, here's what we got.
You know, I had a boss that his famous phrase you can only go from where you're at. Well, this is where we are, right? So you gotta make this poor for this guy in an hour or next week next month How are you gonna do it the best you possibly can for what you have to work with? And that's a challenge that will always be there for ready mix and it's great. It's fun to solve that challenge and learn from it and do it again and then get a chance to do it again and do it again and know you could fall on your face at any given time so
Lee Thrasher (37:31.974)
Be good with it, you know and be good at it
Seth Tandett (37:34.386)
Yeah. Well, like I said, I enjoyed our conversation today. Lee, if folks want to reach out to you, what's the best way?
Lee Thrasher (37:42.882)
Either by email my first initial last name at ctscement.com, lthrasher at ctscement.com, or you can find me on LinkedIn easy enough. Not too many lead thrashers out there.
Seth Tandett (37:56.133)
No, that's how I found them on LinkedIn. All right. All right, Lee, thank you for coming on the podcast today. And folks, until next time, let's keep it concrete.
All right.
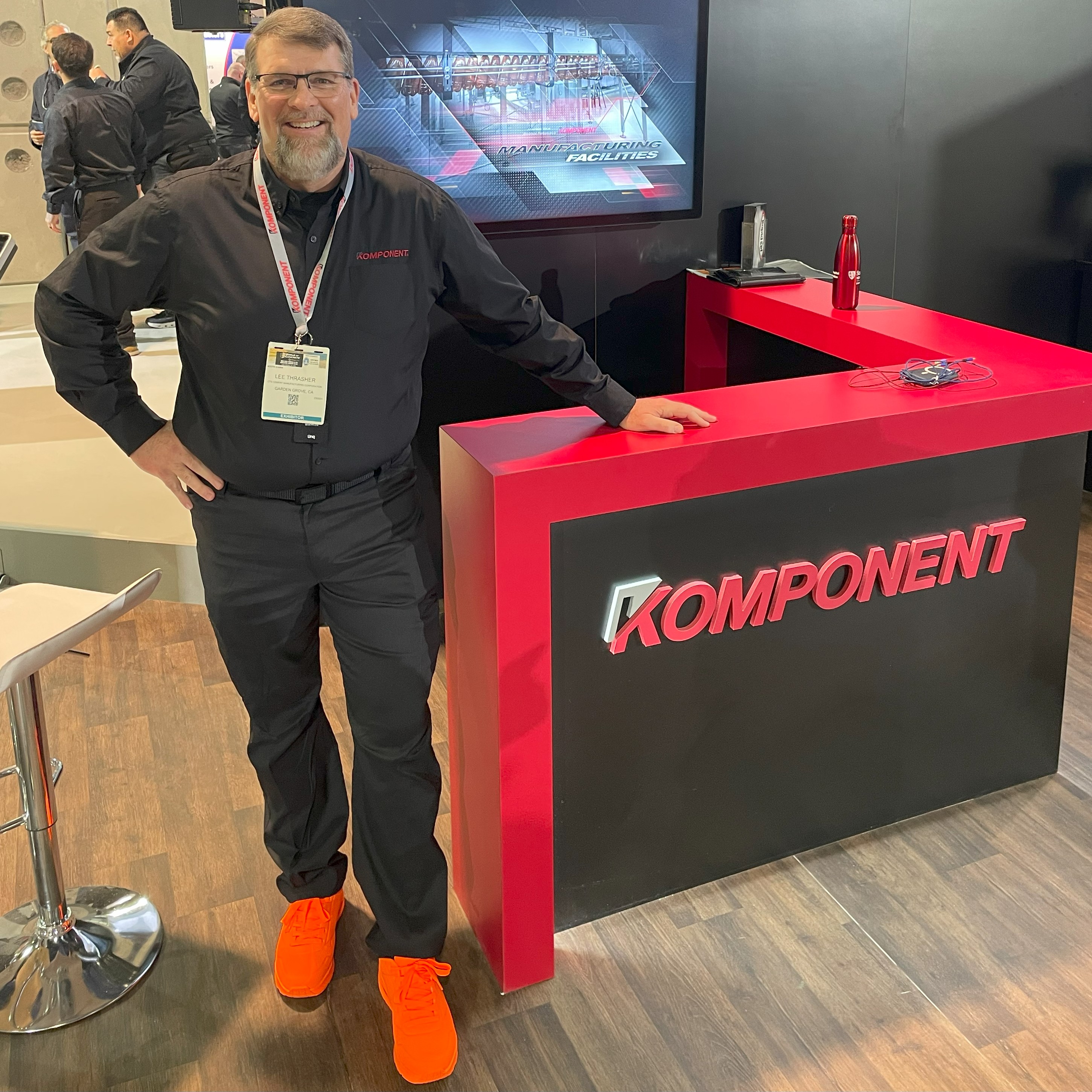
Lee Thrasher
Engineering Sales & Key Accounts
Lee is a genuine concrete enthusiast and represents the Komponent® and Type-K expansive cement products from CTS Cement Manufacturing throughout the Southeastern US in promoting the use of Shrinkage-Compensating Concrete & Enhanced Concrete Mixtures. He has been an active member of the concrete industry for most of his career, both during and after his time earning a degree in Concrete Industry Management from Middle Tennessee State University. He is thrilled to now be working with CTS, founded by one of the industry’s best innovators Ed Rice. Mr. Rice who along with Professor Alexander Klein created today’s Type K Cement and the basis for what has become the shrinkage-compensating concrete market. Ed went on to develop other Belitic Calcium Sulfoluminate (BCSA) Cement products known today under the Rapid Set brand. Lee is a passionate advocate for better concrete, ready-mix producers, industry advancement, implementing specialty & innovative materials into concrete construction, and anything else that involves our greatest building material ever invented – concrete.
He currently serves ACI as the Chair of 329 Performance Criteria for Ready Mix Concrete, is a voting member of 304, 363, and an associate member of 301-J & K, and 330 Technical Committees. Locally, he is a past president of Georgia Chapter ACI and currently serves on the Georgia Ready Mixed Concrete Association’s Technical subcommittee for Design & Control of Concrete to improve adherence to concrete acceptance testing standards. As the Chair of ASTM C09.60 Fresh Concrete Tests and Sub-S…
Read More